The Impact Resistance of Diamond Segment
Diamond saw blade in cutting stone, especially when the depth of the knife is larger, the segment constantly collides with the stone, the collision process, diamond in the diamond segment quickly completed the grinding of the stone, resulting in a large amount of friction, friction is too large, the counter-force of the segment is also greater, this time, if not impact-resistant segment, there will be a fall-off situation. Of course, this situation is less common, in fact, also proved that the diamond segment is good impact resistance, so what makes the segment has such a strong impact resistance? Does this impact resistance have any effect on the segment? For the saw blade cutting process, the segment's strong impact resistance to the cutting how to help? This is what this article is about.
The impact resistance of diamond segment comes from the sintering process of various metal powders of diamond segment, in the sintering process, metal in high temperature and high pressure, atoms into each other, part of the metal began to melt, these melted metal let metal atoms more quickly combined, a variety of metal powders continue to undergo chemical and physical reactions, in this process, metal powder formed a very dense alloy block, such a block not only greatly increased the density of the product, Hardness and impact resistance have also been greatly improved, mainly due to the smaller spacing between atoms and atoms, and various alloys have enhanced the physical resistance of the segment. In summary, the metal alloy in the sintering process, formed a more stable block, with a strong impact resistance, to maintain the segment to stone continuous grinding performance.
Such impact resistance is the stone processing process must have the performance, first of all, denseness can ensure the stability of the structure of the segment, if the structure of unstable segment products, there will be segment deformation, fracture and other conditions, but under the strong impact resistance, the segment structure becomes very stable, as if a bullet, into the stone interior, free completion of the cutting process.
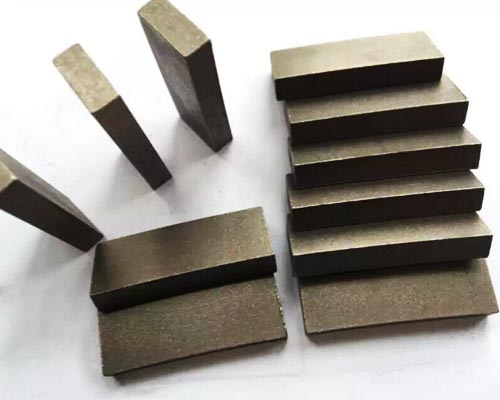
So how helpful is this cutting performance compared to overall cutting? To sum up, there are about the following:
1: to help the base bear greater impact, the segment in the cutting process, if the segment does not have a strong impact resistance, then the impact of the segment will be transferred to the saw blade base, the base body long-term strong impact, will form an early aging situation, resulting in the saw blade substrate needs to be replaced early, increase the production costs of the factory.
2: Strong impact resistance can protect the stone, impact-resistant segment is hit, the segment of the sharp fluctuations, there will be significant fluctuations in the arc cutting pattern, resulting in low yield, or increase the stone layout leveling process, time-consuming and laborious.
3: damage cutting machine, cutting stone process, if the segment can not withstand the impact, swinging saw blade once the knife when the situation of oblique cutting, not only will cut the stone, and the machine also product great harm.
4: The impact-resistant type of the segment can also greatly limit the protection of the welding part, especially the larger part of the weld, the long-term impact will continue to impact the weld, resulting in the weld cracking, the problem of the segment teething.
In general, the current segment products in the impact-resistant performance is better, but there are some segment will be less impact-resistant situation, encounter such a segment, it is best to replace the diamond segment as soon as possible, so as not to appear worse.
Pre:The batching process of diamond segment
Next:Cutting disc basic knowledge about abrasive grain size